Hammer Forge: Precision-Driven Forging Solutions for Industrial Applications
What is Hammer Forging?
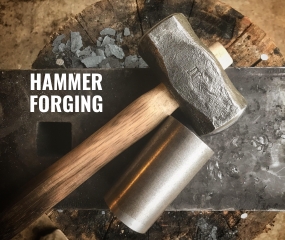
Hammer forging is a manufacturing process in which metal is shaped using compressive force applied by a hammer or a die. This technique is particularly effective for creating high-strength parts that require high precision and durability. The hammer forging process is typically used for producing components that have a high degree of structural integrity and resistance to wear.
At Jay Ambe Industries, we specialize in hammer forging, producing high-quality components that meet the exact requirements of industries such as automotive, aerospace, construction, and heavy machinery.
Why Hammer Forging is Essential for High-Quality Components
Hammer forging provides several advantages that make it an ideal choice for producing industrial components that need to perform under extreme conditions. Here are some of the key benefits:
- Superior Strength: Hammer forging realigns the grain structure of the material, enhancing its strength and durability.
- Improved Material Utilization: This process reduces material wastage, making it more efficient and cost-effective than many other manufacturing methods.
- High Precision: Hammer-forged components are highly precise and can meet strict tolerances required in critical applications.
- Better Toughness: Parts produced through hammer forging exhibit increased toughness and can withstand high levels of stress and pressure.
- Enhanced Wear Resistance: Forged components are more resistant to wear and tear, increasing their longevity and reliability.
Applications of Hammer Forging
Hammer-forged components are essential in industries that demand high strength, precision, and durability. Common applications include:
- Automotive Components: Parts such as gears, crankshafts, and connecting rods.
- Aerospace: Structural components for aircraft that need high strength-to-weight ratios.
- Construction Equipment: Heavy-duty components such as axles, shafts, and gears.
- Industrial Machinery: Parts like bearings, couplings, and industrial tools that experience heavy usage and wear.
Specifications of Hammer Forged Components
At Jay Ambe Industries, we offer hammer-forged components that are built to meet the highest industry standards. Here are the key specifications:
- Materials: Carbon steel, alloy steel, stainless steel, and custom alloys.
- Sizes: Available in a variety of sizes, from small precision components to larger industrial pieces.
- Tolerances: We maintain strict tolerances, typically ranging from ±0.1 mm to ±0.5 mm, depending on the part’s complexity.
- Surface Finishes: Various finishes are available, including matte, smooth, and polished finishes.
- Heat Treatment: Heat-treated to improve mechanical properties like hardness, toughness, and strength.
- Packaging: Components are carefully packaged to ensure protection during transportation and handling.
Why Choose Jay Ambe Industries for Hammer Forging?
Jay Ambe Industries is a leading supplier of hammer-forged components, and here’s why our customers trust us:
- Expertise in Hammer Forging: With years of experience in the forging industry, we have mastered the hammer forging process, ensuring high-quality products.
- Advanced Equipment: We use state-of-the-art forging hammers and dies to produce precise, reliable components for a wide range of applications.
- Customization: We provide tailor-made hammer-forged components to suit the specific needs of our customers, from material selection to part dimensions.
- Quality Control: Every product undergoes rigorous quality checks to ensure that it meets industry standards and performs reliably under pressure.
- Competitive Pricing: Our pricing is designed to offer the best value without compromising on quality, making us an economical choice for businesses.
- On-Time Delivery: We ensure timely delivery of your hammer-forged components, meeting your production schedules and requirements.
Frequently Asked Questions (FAQs) about Hammer Forging
- 1. What is the difference between hammer forging and press forging?
- Hammer forging uses high-impact force to shape the material, while press forging uses continuous pressure. Hammer forging is ideal for producing high-strength, high-precision components.
- 2. What types of materials can be forged using hammer forging?
- Common materials include carbon steel, alloy steel, stainless steel, and special alloys. We can also accommodate custom alloys for specific applications.
- 3. What are the main advantages of hammer-forged parts?
- Hammer-forged parts are stronger, tougher, and more wear-resistant than cast or machined parts. They offer superior grain structure and improved performance in demanding applications.
- 4. Can you customize the size and design of the forged parts?
- Yes, we provide customization options for both the size and design of hammer-forged components to meet your specific needs.
- 5. How is the quality of the hammer-forged parts ensured?
- Quality control is integral to our process. Each hammer-forged component undergoes thorough inspection for dimensional accuracy, surface finish, and mechanical properties.
- 6. How long does the hammer forging process take?
- The duration depends on the complexity and size of the component, but we strive to complete the forging process efficiently while maintaining the highest quality standards.
Verdict: Why Jay Ambe Industries is Your Ideal Partner for Hammer Forging
Jay Ambe Industries has earned its reputation as a leading supplier of hammer-forged components by combining decades of experience with advanced technology and customer-focused solutions. Whether you need components for the automotive, aerospace, construction, or industrial machinery sectors, our hammer-forged components provide superior strength, precision, and durability.
With an unwavering commitment to quality, competitive pricing, and timely delivery, we’re the trusted partner for all your hammer forging needs. Let us help you achieve excellence in manufacturing by providing the highest quality components tailored to your exact specifications.